Heavy fuel oil (HFO) supply solutions
- Fast, easy installation delivered through a compact design and versatile connections
- Easy operation: all important displays and instruments are visible at a glance
- Long and extremely reliable service life from quality components, carefully chosen materials and advanced manufacturing
Felexible installations, easilly maintained
To supply HFO for main and auxiliary engines
- Cost-savings through standardised components
- Easy maintenance: access is only required at the front and right-hand side of the unit
- Maximum power serviceable: approx.10MW
- Standard option comprises separate feeder and booster components
- Flexible component arrangements for the space available
- Dimensions, including service space: 1.50m x 2.90m
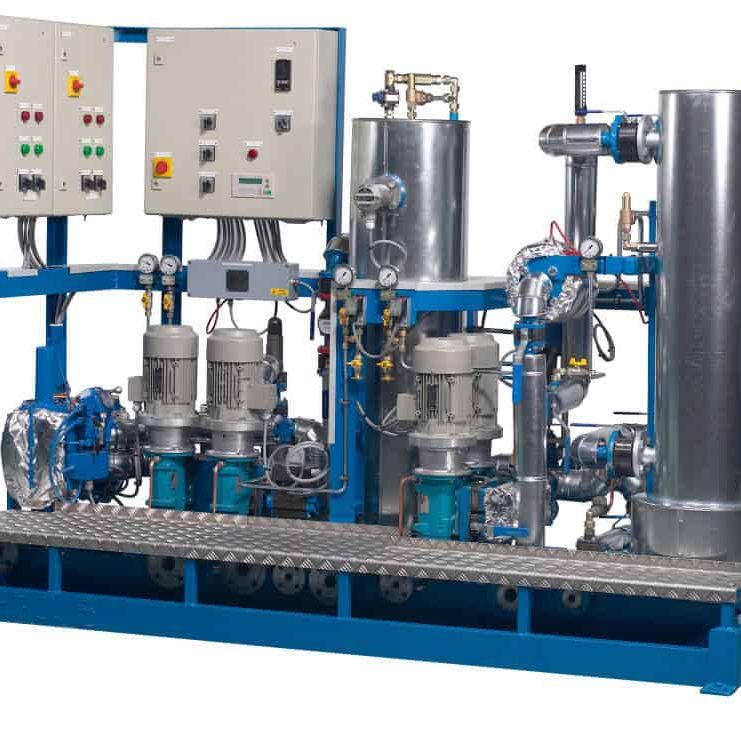
Customer specific solutions with Auramarine AMB-M-series
We work in close co-operation with customers and engine manufacturers to develop the best system configuration for every project. Fuel supply units from our AMB-M-series can be extensively customised to meet all fuel-conditioning needs. Depending on system requirements, they can be configured to accommodate Auramarine’s wide range of heaters, coolers, flow-meters, marine diesel oil and marine gas oil emergency pumps, homogenisators and additional filters.
All AMB-M units are designed to reliably and simultaneously supply fuel to both main engine and auxiliary engines.
AMB fuel oil supply units, also known as feeder-booster or circulation units, have versatile pipe connections fitted at the rear and front to enable easy installation. As standard, to meet any changing needs, it is possible to add new or extended functions at a later date.
All our units combine proven accessibility with ease of maintenance, from the service space around the unit to the user-friendly location of all displays and instruments. This extends to the horizontal location of heavy fuel oil heaters.
Auramarine HFO solutions consists of:
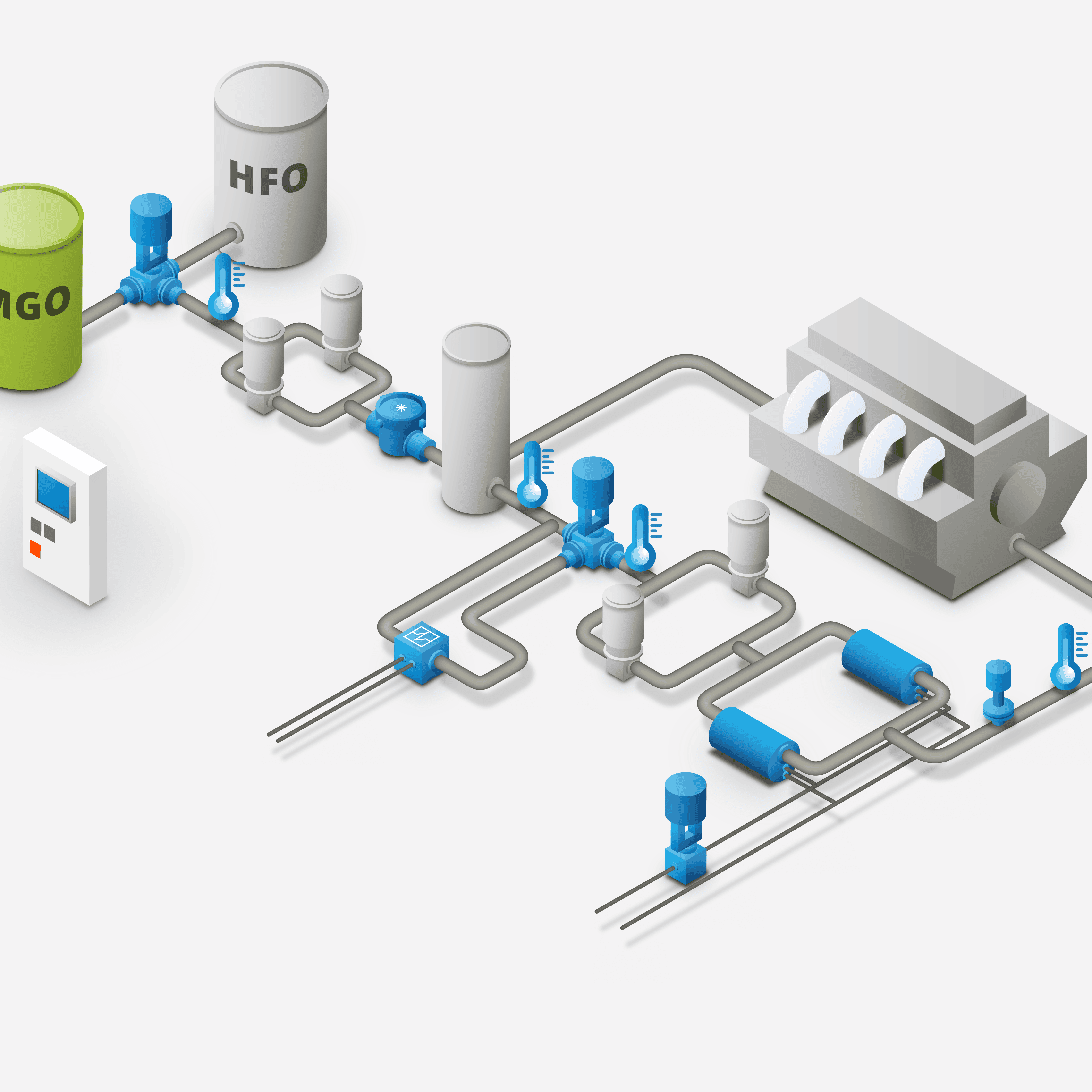
operator's fuel choice depends on trade routes
HFO and MGO
- Coolers and in certain circumstances chillers, are needed to reach and maintain the correct MGO viscosity for main and auxiliary engines.
- A fuel pump's ability to accommodate specific fuels should be evaluated. To ensure the correct fuel viscosity, upgrades may be necessary to guarantee pumping capacity and lubricity.
- Fuel transfer and circulation pumps with higher thresholds for leaks or blockages, caused by the varying lubricity of fuels, will also improve long-term cost-efficiency and operational availability.
- Fuel filters should be able to remove cat fines and alert operators about frequent back-flush cycles or clogging.
Fuel properties and challenges
Conventional heavy fuel oil, with a maximum sulphur content of 3.50%, can only be used on ships that are equipped with exhaust gas scrubbers. Calls in certain ports may require further steps to achieve compliance, including the switch to low-sulphur fuel.
Low-sulphur content HFOs can be used without a scrubber. However, as result of blending different fuels in the production and delivery chain, such fuels may not be tested or evaluated properly. Although, for example, the ISO 8217 standard is in place, there are practical concerns about how to assess fuel compatibility or obtain accurate data describing fuel properties.
Even if delivered as a stable product, blended fuels can become unstable if they mix with other fuels.
Very often especially the fuels with low asphaltene content are subject to stability and compatibility issues, and clogging of asphaltene in the oil, which can cause severe problems and even engine failures on board. Auramarine's PORLA analyser fulfills the need for an easy, reliable and fast analysis instrument to ensure the stability and - when mixing fuels - the fuel compatibility and the recommended mixing order.
MGO may have lower viscosity than the fuels for which the ship s fuel system was originally designed.
Fuel changeover systems support scrubber operations
In open seas, conventional HFO combined with a scrubber, will ensure IMO 2020 compliance. When approaching ports with stricter environmental standards, for example zero discharge of wash water effluent, operators may need to switch off the scrubbers and switch between different fuels. The need to engage the fuel changeover system may also occur if the scrubber malfunctions. Auramarine’s automated fuel changeover system can act as an emergency changeover system to secure continuous operation.
To safeguard the troublefree operation of the main and auxiliary engines during changeovers between different sulphur-content fuels, we recommend Auramarine's automated fuel changeover system, which combines the changeover with automated cooling and viscosity control, optimising and controlling fuel changeovers.
A timely, controlled and accurate fuel changeover makes sense both from an operational and economical point of view. With a manually controlled fuel changeover system it is extremely challenging to simultaneously maintain the correct fuel temperature change rate and viscosity at all times. A smart, automated changeover system safeguards compliance and uninterrupted engine operation, and at the same time minimises the periods that the engines must run on, currently more expensive, MGO.