Solutions for Methanol operations
WHAT IS THE ANNUAL COST OF WATER IN METHANOL?
Learn more on how to monitor methanol water content with Auramarine water content analyser.
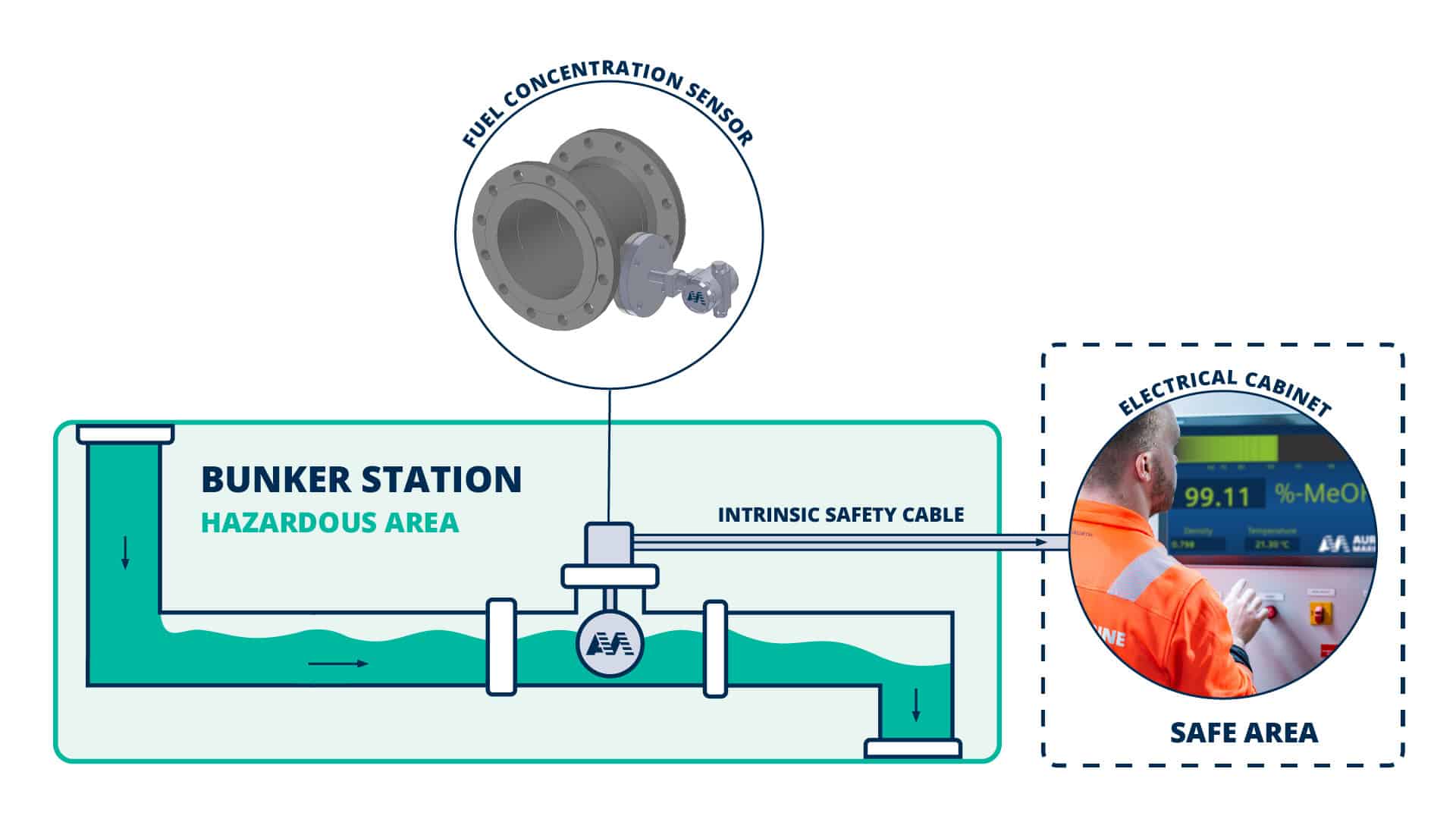
Our methanol system is equipped with complete automation
The Auramarine Methanol Supply System supplies methanol to the Master fuel valve while regulating the flow, pressure, and temperature of the methanol. With this regulation, combined with filtration, we can ensure that the system suits most types of engines and other methanol consumers. The system actively maintains the supply pressure within specified tolerances during load changes and meets strict safety requirements.
The system supplies methanol from the bunkering station to the engines and other consumers. It supports efficient onboard arrangement and fits the available space. The Auramarine methanol system suits both two-stroke and four-stroke engines.
Combining the best of nature and technology
We base our systems on clean and renewable fuels. Auramarine’s state-of-the-art methanol fuel supply systems are modular and efficient, while ensuring safety, reliability, and continuity by combining the best of both nature and technology.

A viable option for decarbonisation
Methanol is one of the most viable clean fuels to cut greenhouse gas emissions and help meet global decarbonisation targets. Indeed, full carbon neutrality can be achieved by using "green methanol". Methanol also reduces other emissions such as SOx, NOx, and particulates compared to diesel oil.
Considering the energy efficiency design (EEDI) and emissions reduction requirements, methanol is a viable option as a maritime fuel.
Auramarine methanol fuel supply system includes:
- Fuel supply to consumer
- Fuel consumption measurement
- Pressure control
- Temperature control
- Filtration
- Shut-off valves for safe maintenance
- Automatic draining and inerting
- Fuel valve train and water injection as option.
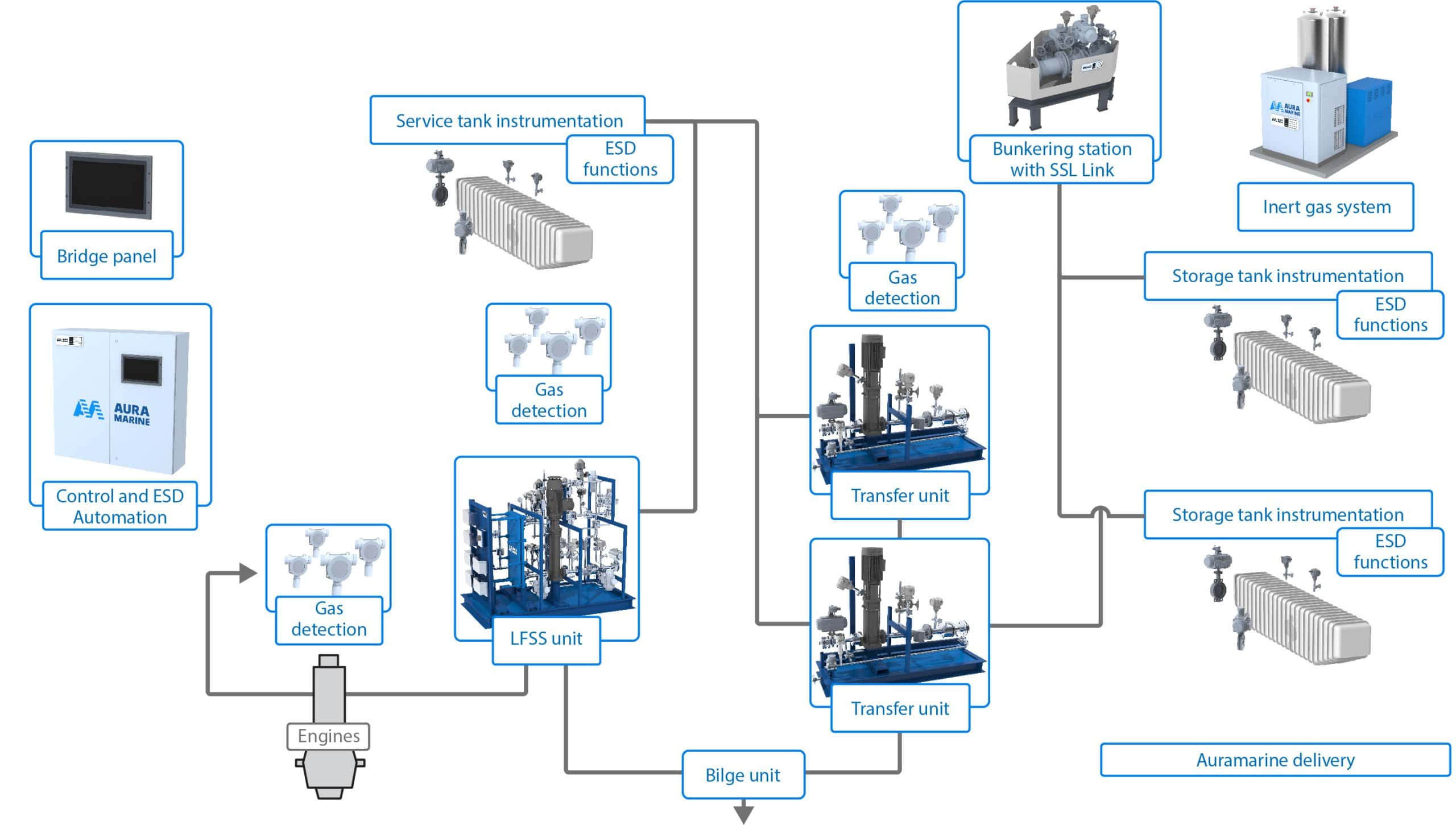
Methanol fuel supply system safety
All fuel supply system materials and manufacturing procedures need to be suitable for methanol service and for the specifications of a particular application. Because of this, we have designed the unit to fit on closed and Ex rated hazardous areas. All IECEx and Health and Safety Guidelines (HSE) have been taken into account.
This level of safety is achieved by using a self-draining mechanical design in conjunction with the nitrogen inerting process and double block and bleed configurations to any serviceable methanol line segments. Additionally, all of our components and electrical equipment are specially selected for use in a hazardous area.
In order to minimize the electrical equipment in a hazardous area, our team has designed the electrical cabinets, control panels and variable frequency drives to be fitted separately to a safe area.
Seamless backup for methanol operation
For dual fuel engines operating on methanol, our units always have a backup system that kicks in immediately if a disturbance is detected in the methanol combustion.
Because Auramarine HFO and MGO units are built to always maintain the engine-specific fuel temperatures and other requirements, these units are suitable for backup purposes and they are already trusted and proven in current LNG-operated vessels.
When selecting the methanol fuel supply system, backup fuel system and pilot fuel system from same supplier, the following synergies and benefits accompany it:
- Smoother project administration for shipyard at the shipbuilding stage
- The design can be optimized for the exact space available
- All documentation is from one supplier at the same way
- One contact point for all the equipment
References
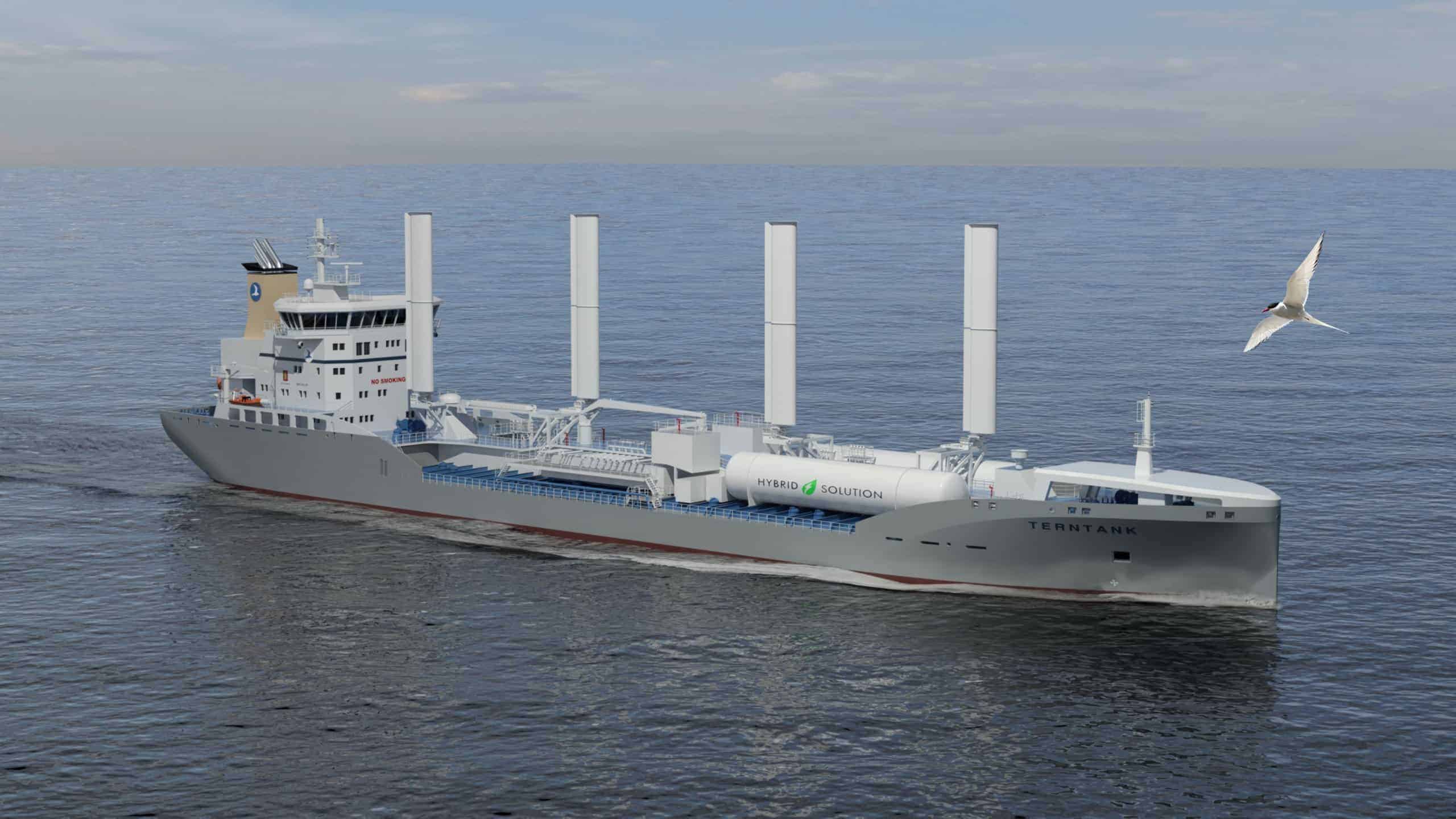
Terntank tankers
Terntank's ships are built at China Merchants Jinling Shipyard (Yangzhou), hulls CMYZ0129-CMYZ0131, with the first vessel of the series to be delivered in March 2025.
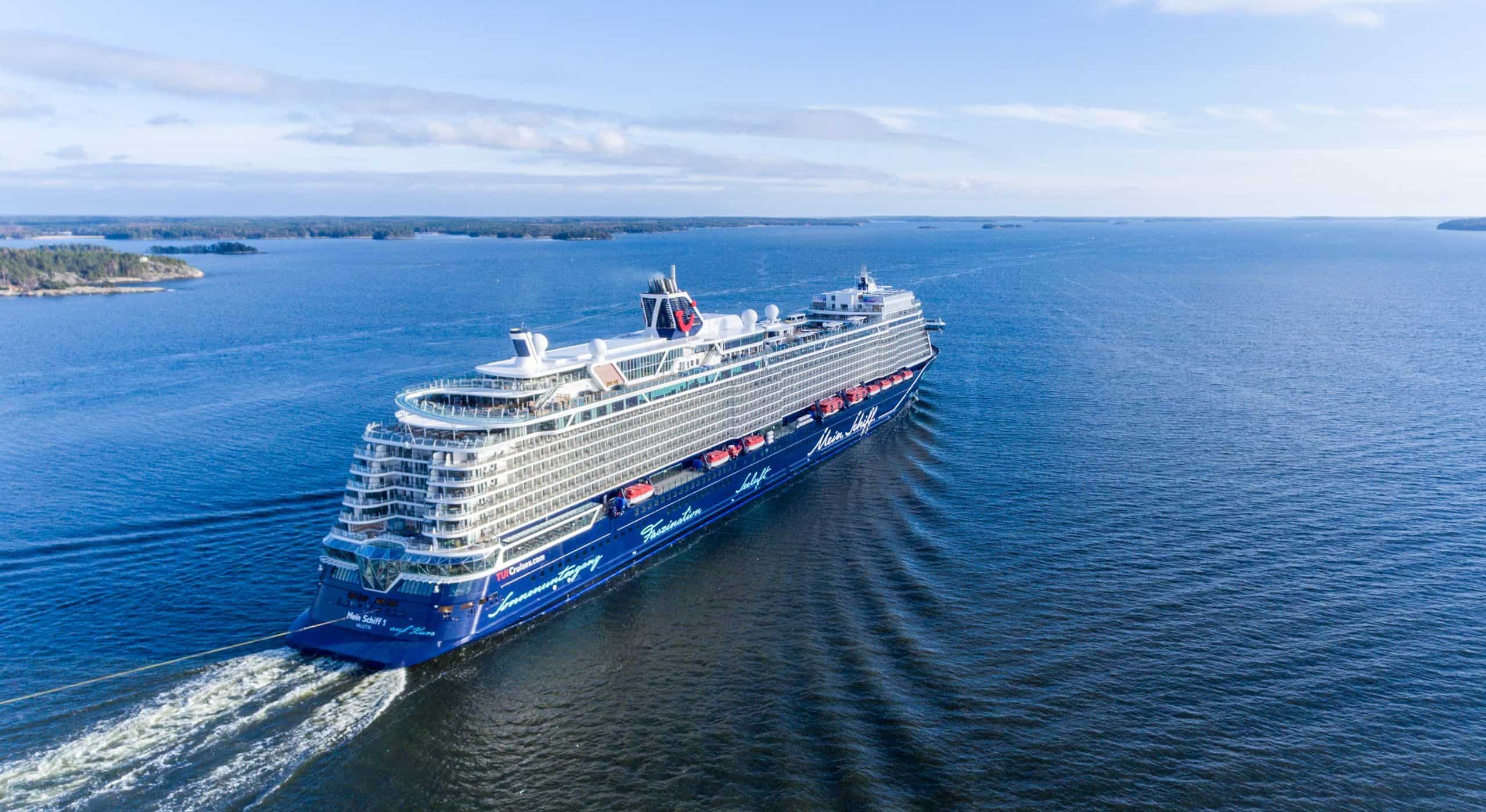
Mein Schiff 7
Mein Schiff 7 is a state-of-the-art vessel that prioritises sustainability and efficiency. With a length of 316 meters and a width of 35.8 meters, it can accommodate nearly 2,900 passengers and 1,000 crew members.