Ensuring continuity and compliance
A hands-on approach to spare parts management; knowledge, not assumption
At the height of the COVID-19 pandemic, the International Ship Suppliers and Services Association (ISSA) called for ship suppliers to be given ‘essential worker’ status to enable them to keep the world’s commercial vessels stocked with all vital supplies and spare parts. They stressed the importance of keeping supply chains moving, both in terms of shipping critical supplies and goods to where they are needed, as well as keeping the heart of a ravaged global economy still beating no matter how weak. This was a message reiterated by the IMO and the United National Conference on Trade and Development (UNCTAD) in June, when they issued a joint statement calling for collaborative action to keep vessels moving, ports open, and cross-border trade flowing during the pandemic.
The importance of keeping supply chains moving
The message from ISSA and IMO/UNCTAD naturally focused on ensuring crew changeovers could be facilitated, and that they had food and supplies to keep them healthy while at sea for many months. However, the availability of spare parts, in relation to the operational continuity of a vessel, was also of critical importance; particularly in the current dynamics, the wellbeing of crew and the smooth running of vessels could not be compromised.
Entering the new decade, the shipping industry faced its greatest challenge since moving from coal to oil as the choice of propulsion, with IMO2020 dominating the majority of media headlines and many a boardroom agenda. While adopting the right and most cost-effective solution was the main concern up until enforcement on 1st January 2020, the industry then moved focus onto the operational challenges that compliance potentially brings. Throw a global pandemic into the mix, and the potential threat to supply chains as a result of unplanned vessel downtime became increasingly important
Managing the complexities of fuel switching in an IMO2020 world
Having access to the right, operationally critical spare parts has always been crucial, and a mainstay of best practice standards – such as OCIMF’s (Oil Companies International Marine Forum) Safety Critical Equipment and Spare Parts Guidance. However, the complexities of moving to new hybrid very low sulphur products (the main choice for compliance) due to the variable and wide-ranging viscosities in the market, and their relatively unknown properties, presents new challenges for every vessel owner and operator. And it requires making developments to fuel supply systems, the proper function of which is critical for a vessel’s power and propulsion.
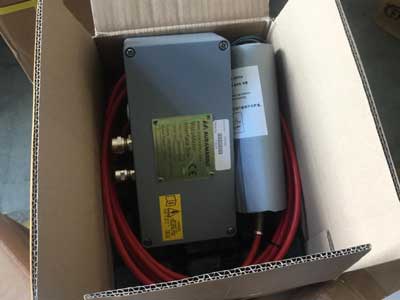
A new Auramarine viscometer ready for installation.
For example, it is difficult to simultaneously keep the fuel temperature change rate low enough and the viscosity high enough at the engine inlets. Injection pressure losses caused by too low a viscosity may also result in difficulties during start-up and low-load operations. In addition, too low a viscosity reduces the fuel’s effectiveness as a lubricant, which can lead to malfunctions of fuel pumps and other machinery. Likewise, interruptions in fuel supply during the changeover process can also lead to reduced engine power or loss of propulsion. It’s not exactly straight forward! Which is why our fuel changeover system, FuelSafe, handles all these challenges at the push of a button, including control optimisation for heaters and coolers.
A strategic approach to spare parts management
In 2020, it is critical that owners and operators have this kind of system in place, and that they also have an integrated and strategic approach to managing spare parts in order to repair, modernise, and upgrade systems and components. Of course, Auramarine’s fuel supply systems are designed with back-ups for all critical elements, however, we also ensure our customers have rapid access to the spare parts that they need, when and where they need them – which is a fundamental part of our ongoing customer support and relationship management service.
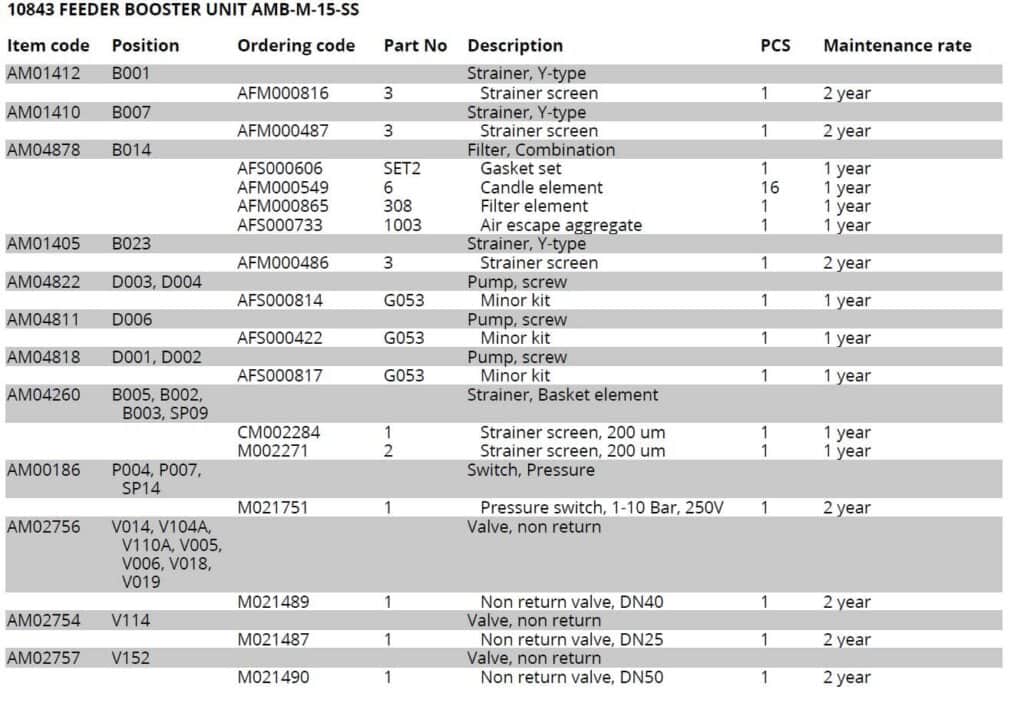
Driven by our Lifecycle services team, our focus is on ensuring that all elements of a fleet’s spare parts network are catered for. This enables owners and operators to swiftly continue operations whilst staying in line with regulations, as well as giving them peace of mind, because their operations are safeguarded, even in unforeseen circumstances. As part of this offering, we introduced an application that assesses a customer vessel’s spare parts requirements for a specific period, and automatically provides the customer with a bespoke spare parts kit for each specific fuel supply system; a strategy that is based on an in-depth knowledge of spare parts consumption, not just assumption.
Driving operational performance and efficiency in the most challenging market dynamics
With continuing changes to the regulatory landscape, and COVID-19 impacting operators in different ways depending on location, it is critical that spare parts programmes are tailored for specific ship owner requirements. While it might be difficult to stay ahead of the curve in today’s uncertain climate, proactive and planned maintenance is vital to protecting critical equipment, as well as upgrading and modernising systems to provide superior performance, drive efficiencies, ensure compliance, minimise downtime, and provide peace of mind. These commodities have always carried a high premium, but they’re even more important in these unprecedented times.
By Kalle Koivusalo, Area Sales Manager for Spare parts at Lifecycle services, Auramarine
Find out how Auramarine can support your spare parts management: Auramarine spare parts.